Introdução
Há dois processos diferentes para aplicação de um revestimento de zinco ao aço através do método de imersão a quente. Ambos envolvem a imersão do aço em um banho de zinco fundido. Visto que o zinco derrete a 787ºF [419ºC], e deve depois ser aquecido a uma temperatura de aproximadamente 850ºF [455ºC] ou maior para que o processo de galvanização seja efetivo, ambas as operações são referidas em geral como processo “por imersão a quente”.
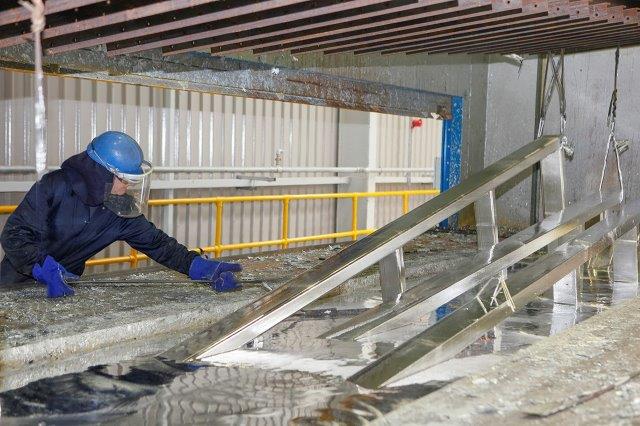
Um processo envolve a aplicação de zinco sobre uma tira contínua de chapa de aço à medida que ela passa pelo banho de zinco fundido em alta velocidade – logo, o termo galvanização por imersão a quente “contínua”. À medida que uma bobina é processada através da linha de revestimento, outra é soldada à sua ponta final. O processo é verdadeiramente “contínuo”, já que a linha pode operar por dias sem interrupção. O outro processo envolve a aplicação de um revestimento de zinco na superfície de peças de aço após elas terem sido fabricadas. Não é contínuo, pois as peças são imersas em “batelada” no banho de zinco; logo, os nomes “por batelada”, “pós-fabricação” ou galvanização “geral” – termos que são usados alternadamente. Peças pequenas como fechos e grandes como vigas estruturais de pontes, são galvanizadas pelo método por batelada.
Galvanização Geral (Batelada ou Pós-Fabricação)
O segundo processo por imersão a quente envolve a aplicação de zinco sobre um formato “fabricado”. Isso significa que o aço é conformado em produto final – uma viga estrutural, um tubo de grande diâmetro, ou um pequeno fecho – e depois é mergulhado no zinco fundido para aplicação do revestimento de zinco. Estes itens são revestidos um de cada vez ou, em caso de peças pequenas, diversas peças de uma vez, contidas em uma “cesta”. Portanto, os termos “batelada” ou “pós-fabricação” são utilizados para descrever esses processos.
De certa forma, o processo geral ou por batelada é igual ao processo contínuo, já que o objetivo é aplicar um revestimento contínuo de zinco resistente à corrosão sobre a superfície do aço. Entretanto, estes dois métodos têm muitas diferenças. O processo por batelada é ilustrado na figura abaixo.

O processo por batelada típico envolve três passos anteriores à imersão de peças no banho de zinco fundido:
– Limpeza cáustica
– Decapagem
– Fluxagem
Limpeza cáustica envolve a utilização de uma solução alcalina quente para remover contaminantes orgânicos, como óleos e graxas. Estes contaminantes de superfície precisam ser removidos antes da decapagem, para que a superfície possa ser “molhada” por uma solução de decapagem.
Decapagem envolve a imersão de peças em uma solução ácida (frequentemente ácido sulfúrico aquecido ou ácido hidroclorídrico em temperatura ambiente) para remoção da carepa ou ferrugem da superfície (ambos são óxidos de ferro). O termo “carepa” é geralmente utilizado para descrever óxidos de ferro que são formados em altas temperaturas, como durante a laminação a quente, recozimento no ar ou soldagem.
Ferrugem é o produto da corrosão da superfície do aço quando molhada. Ambos os tipos de óxido de ferro precisam ser removidos antes da aplicação do revestimento de zinco.
Fluxagem envolve a aplicação de um revestimento químico especial sobre a superfície da peça de aço. Este “fluxo” serve para o mesmo propósito dos fluxos utilizados durante as operações de soldagem. A substância química fundente (cloreto de amônia e zinco) é designada para remover quimicamente os últimos vestígios de óxidos antes que a imersão do aço no zinco fundido ocorra, permitindo que o aço seja molhado pelo zinco fundido. A fluxagem pode ser tanto “seca” quando “molhada”. A fluxagem seca envolve a imersão da peça de aço em uma solução aquosa defluxo. Ao removê-la, a solução de fluxo é seca antes da imersão no banho de zinco. (Note que há um processo de galvanização contínua que utiliza a fluxagem seca. Ele está descrito na GalvInfoNote 2.7). Na fluxagem molhada, uma camada líquida de cloreto de amônia e zinco (fundido) flutua por cima do banho de zinco fundido. A peça a ser revestida é então imersa no fundente à medida que ela vai sendo introduzida no banho de revestimento. (A fluxagem molhada funciona pelo fato de que o cloreto de amônia e zinco possui um ponto de derretimento abaixo do ponto do zinco fundido, além de ser menos denso do que o zinco fundido, deste modo flutuando na superfície do banho).
Assim como na galvanização contínua, a aplicação do revestimento de zinco em uma galvanização por batelada envolve a imersão de aço em um banho de zinco fundido. Porém, ao contrário do processo contínuo, em que o aço é imerso por um breve período de tempo, o processo por batelada requer que a peça seja imersão por períodos de tempo bem maiores, medidos normalmente em minutos, não em segundos. Há duas razões para a necessidade de períodos de imersão mais longos. Uma delas é permitir que a peça alcance a temperatura do banho. A imersão de um tubo grande com paredes grossas relativamente frias, por exemplo, resulta em uma película de zinco com temperatura de superfície muito baixa ao ser imersa. Para que o revestimento se una metalurgicamente ao aço, o tubo precisa alcançar a temperatura de banho para “derreter” o zinco. Depois, é necessário um tempo adicional para desenvolver a zona de ligação da liga de ferro/zinco.
Ao contrário do processo contínuo, onde a camada de liga tem que ser mantida muito fina para acomodar a conformação subsequente na forma final, no caso de peças galvanizadas por batelada, a camada da liga pode ser mais espessa. Na realidade, uma camada de liga mais espessa é normalmente desejada para proporcionar um tempo de vida mais longo ao produto final, isto é, um tempo maior antes do aparecimento de ferrugem. Como o próprio zinco, a camada de liga protege galvanicamente a peça de aço e uma camada de liga mais espessa significa uma vida mais longa. Sim, a camada de liga é dura e quebradiça, mas visto que a peça já está fabricada, não haverá mais conformação adicional que possa rachar a liga. A camada de liga quebradiça não é deletéria. Isso não resultará em danos no revestimento durante o envio e manuseio posterior em canteiros.
Uma micrografia representativa da camada de liga que se forma enquanto o aço é imerso no banho é mostrada na Figura 1. Como pode ser visto nesta foto, a camada de liga é quase 50% da espessura do revestimento total, que na verdade consiste de duas ou mais camadas de zinco/ferro. Cada uma dessas camadas distintas se combina para formar a zona de camada de liga “total”.

Na verdade, cada camada tem uma quantidade específica de ferro e zinco. A camada mais próxima do aço tem a maior quantidade de ferro enquanto a camada imediatamente adjacente à camada externa de zinco puro tem a quantidade mais baixa de ferro. A composição e as propriedades dessas camadas de liga são mostradas na Tabela 1.
Lembre-se que a camada de liga aumenta através de uma reação de difusão mesclada entre os átomos do aço e zinco. Este é um processo que depende de tempo e, para a maior parte dos aços, um tempo maior de imersão proporciona uma camada de liga mais espessa. Na realidade, para peças galvanizadas por batelada, um tempo de imersão adicional é frequentemente necessário para atingir a espessura final exigida do revestimento protetor (a espessura é uma combinação entre a camada de liga e o metal de revestimento externo de zinco puro).

Como resultado dos longos períodos de imersão, a espessura final do revestimento (zinco puro + camada de liga) em peças galvanizadas por batelada é bem mais espessa do que o revestimento em uma chapa de galvanização contínua – pelo menos, a espessura pode ser muito mais grossa se for desejado/solicitado. Esta é a maior diferença entre o processo de galvanização por batelada e o processo de galvanização contínua.
Há questões de produção que geralmente precisam ser consideradas com respeito à espessura máxima de camada de liga que pode ser atingida durante a galvanização por batelada. À medida que a camada de liga se torna mais espessa, o seu índice de crescimento fica mais lento, pois a difusão através do espessamento da camada da liga leva mais tempo, o que resulta num limite prático para a espessura final. Além disso, para algumas composições de aço, a união de liga com espessura uniforme não se forma na superfície. Em vez disso, a liga cresce até uma determinada espessura e depois começa a criar lascas na superfície do aço. Quando este tipo de comportamento é encontrado, a espessura máxima de revestimento é menor do que quando a liga continua a crescer como uma camada compacta.
Composição de Banho de Zinco para Galvanização Geral (por Batelada)
Historicamente, o banho de zinco utilizado para galvanização geral contém entre 0,5 e 1,0% de chumbo. O chumbo possuía dois efeitos. Primeiro, causava a formação da típica, atraente e grande superfície de flor de zinco, que através dos anos foi “o modo de identificar revestimentos galvanizados”. Segundo, o chumbo foi benéfico para acomodar “drenagem livre” de zinco em excesso, à medida que a peça era removida do banho de zinco. Em alguns casos atuais, o bismuto está sendo substituído por chumbo para alcançar a drenagem livre do excesso de zinco. Ligas que contém bismuto para a utilização pela indústria de galvanização geral estão disponíveis hoje através de vários fornecedores de zinco.
Atualmente, outra adição de liga ao zinco que está recebendo atenção como uma maneira de melhorar ainda mais o desempenho do revestimento é a adição do níquel ao banho de galvanização. A influência do níquel é importante com relação ao desenvolvimento da camada de liga de zinco/ferro, especialmente ao galvanizar aços com alto teor de silício. Este desenvolvimento é relativamente novo e os aspectos metalúrgicos relacionados à adição de pequenas quantidades de níquel ainda estão sendo descobertos.

A adição de 0,15 a 0,20% de alumínio ao banho de revestimento – uma adição necessária no caso de banho em galvanização contínua – não é uma prática típica nos casos de galvanização geral. Na galvanização geral, o desenvolvimento de uma camada de liga espessa é importante para a obtenção da espessura do revestimento exigida. O alumínio age como um inibidor e interfere nesta ação.
Espessura da Peça
Outra diferença nestes dois processos, por batelada vs. contínuo, está relacionada à espessura do aço que pode ser galvanizado sem a ocorrência de “distorção quente” do aço. No processo contínuo, o aço muito fino pode ser revestido. A razão para que isso possa ser feito é que durante a galvanização contínua, a chapa de aço é mantida sob um pouco de tensão enquanto está sendo processada. A tensão precisa ser aplicada para “arrastar” a faixa de aço pela linha de revestimento e manter o nivelamento da chapa. A distorção da chapa pode ocorrer durante a exposição às altas temperaturas de recozimento. A tensão previne a distorção, e permite uma aplicação regular e controlada do zinco sobre a chapa muito fina, que de outra forma não seria possível se ela não fosse plana.
No processo por batelada, os produtos imersos em um banho de revestimento não são comprimidos pela ação de forças externas. A peça tem que ser projetada para ser dimensionalmente estável durante a exposição à temperatura do banho. Isto é realizado através da utilização de aços mais espessos e pelo projeto de peças que previnem distorções geradas pelo calor. Além disso, reforços temporários podem ser utilizados para peças com paredes finas para minimizar as distorções causadas pelo aquecimento. Resumidamente, não é fácil galvanizar por batelada peças fabricadas com chapa de aço fino, da mesma forma que também não é fácil a galvanização contínua de chapas de aço pesadas.
Para a especificação da galvanização por imersão a quente geral (por batelada), conhecida também no mercado como galvanização a fogo, recomenda-se utilizar a norma ABNT NBR 6323 – Galvanização por imersão a quente de produtos de aço e ferro fundido ― Especificação.
Maiores explicações sobre o processo de galvanização geral pós-fabricação, vá ao site da The American Galvanizers Association em www.galvanizeit.org/ ou acesse ao “Manual para Especificação da Galvanização por Imersão a Quente – 2017 disponível no site do ICZ – www.icz.org.br
Trabalho elaborado pelo IZA – International Zinc Association, GalvInfoNote 2.3 e traduzido e adaptado por Departamento técnico do ICZ –http://www.icz.org.br.
Nota do Editor: O artigo sobre galvanização por processo continuo, foi apresentado na edição 151 da revista Siderurgia Brasil.