A fabricação de tubos e perfis de aço requer cuidados redobrados no controle de custos, uma vez que qualquer tipo de desvio e a inobservância de parâmetros bem definidos podem ocasionar sérias perdas.
Condemir Silva Filho*
ENTÃO, O QUE FAZER PARA MELHORAR A PRODUTIVIDADE?
A “coisa” parece complicada. Mas, na realidade, é bem simples resolver os excessos de paradas, o que, entretanto, nem sempre é verdade para as “perdas ocultas”. Porém, basta haver regras claras e disciplina no seu cumprimento, e ter sempre em mente que os setores de Apoio devem trabalhar para que as máquinas tenham o máximo de disponibilidade de tempo para a operação.
Começando pelo PCP, a boa prática diz que existe um lote mínimo para se produzir um produto. E isso deve ser fechado entre os setores de Produção, Técnico e Comercial. Caso contrário, os custos podem inviabilizar a produção de um determinado produto. Também se deve respeitar a sequência de produção, porque alguns produtos necessitam entrar em máquina antes de outros. Por exemplo: em uma formadora de tubo, uma espessura baixa (<1,20 mm) não consegue empurrar uma espessura alta (>4,75 mm).
Além disso, o PCP também deve respeitar os padrões de matéria-prima, largura de fita e as perdas mínimas no corte de bobinas, evitando assim transferir os desvios de qualidade (perdas) para os processos posteriores. Nunca se deve, por exemplo, iniciar a bitola com uma matéria-prima de espessura alta ou de alta resistência. O programa de produção deve considerar os rolos de fita provisionados adequadamente às Ordens de Produção, tanto em qualidade do aço quanto em quantidade.
PROBLEMAS DE MATÉRIA-PRIMA
Os “problemas na matéria-prima” ocorrem por má especificação, ou má aplicação do aço no produto. Normalmente, o setor Técnico sequer foi consultado, programando-se o processamento da matéria-prima “divergente” – ou, simplesmente, “diferente” – junto com as outras, “costumeiras”, sem avisar esse setor.
Por sua vez, a Produção deve ter um programa bem definido, e seu gestor deve confiar nele, de modo a cumpri-lo com segurança. Se houver variações da matéria-prima, estas devem ser agrupadas e processadas em lotes de mesma natureza, a fim de prevenir excessos de ajustes. A Produção deve ainda respeitar os padrões de montagem – ou seja, o Plano de Montagem – da máquina, e este deve estar atualizado pelo setor Técnico. E, sim, é fato que o uso de um Plano de Montagem reduz o tempo de setup, além das perdas! Por outro lado, os documentos de Produção (Ordem e Registros de Produção e Qualidade) devem conter todas as informações essenciais para o processo, e serem previamente analisados pelo gestor da Produção, a fim de que quaisquer divergências sejam sanadas antes de chegar ao operador.
À Manutenção cabe a missão dupla de impedir que as paradas ocorram. E, caso ocorram de forma não programada, que tais interrupções sejam rápidas e efetivas, para evitar sua reincidência. Para tanto, uma estreita sintonia entre o gestor da Produção e do PCP tem que existir. Paradas mais longas podem afetar a entrega e, ao mesmo tempo que soluções sem análise podem trazer consequências fatais não só para o cliente, mas também para o equipamento. E é importante ressaltar que parte da Manutenção é corretamente efetuada pela própria Produção, como no caso de trocas de insumos (serras, ferramentas, insertos e até alguns rolamentos), além da lubrificação feita principalmente no setup. E vale ainda lembrar que “A formadora de tubo é como um porta-ferramenta. Quando os encostos dos eixos estão fora de alinhamento, ficam fora também as ferramentas montadas neles!” [1] (Ver figuras 1 e 2).
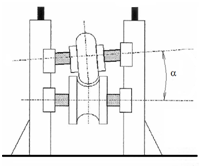
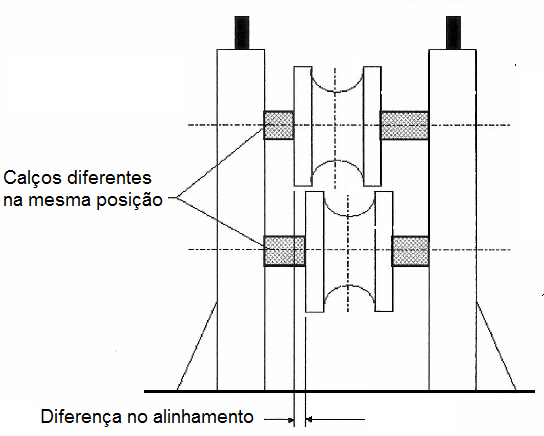
Figura 1 – eixos inclinados Figura 2 – encosto desalinhado
MATERIALIZANDO O “SONHO” DA PRODUÇÃO
Ter um Almoxarifado com todos os componentes de manutenção e insumos de produção é um sonho de qualquer gestor de Produção. Mas, isso é impossível. Então, temos que confiar nos manuais dos equipamentos e em suas listas de peças de reposição. É claro que para esses componentes, deve-se manter um estoque de segurança e uma boa política de reposição. E quanto aos insumos (consumíveis), não é necessário dizer que eles têm obrigatoriamente de estar disponíveis à Produção, sob pena de não haver produção sem eles! Cabe lembrar que, entre os insumos, podemos considerar as ferramentas de conformação que se desgastam com o tempo, tais como rolos de solda e discos de guia (discos de fin-pass). E o uso de alternativos como “quebra-galho” só deve ocorrer em casos de extrema exceção, senão isso pode se tornar um vício ao qual todos acabam se acostumando. Em outras palavras, ninguém dará mais valor ao correto abastecimento de componentes.
A seu turno, geralmente o setor de Compras de insumos sempre aparece com itens de preço mais competitivo em relação aos insumos já consagrados. E isso é ótimo: tem que ocorrer. Mas preço não é tudo: é preciso avaliar os custos, isto é, o quanto de valor é agregado ao produto, considerando a qualidade final, a durabilidade, a segurança, e assim por diante. Em conjunto com o de Produção, osetor Técnico tem condições de fazer essa avaliação de rendimento e custos. E veja que evitei aqui usar o termo “Custo x Benefício”, pois acredito que sua aplicação geralmente resulta em baixa qualidade. Uma pastilha (inserto) de remoção pode custar metade do preço de outra, mas quebra depois de 20 barras de tubo, gerando refugo de três ou quatro barras. E isso se o operador for rápido!
Por fim, vale um comentário também para a Manutenção que utiliza rolamentos de segunda qualidade, pois, nessa situação, se pensou apenas no preço. Assim, seguir as especificações é a função de qualquer gestor de Manutenção. E, em casos excepcionais, não custa nada consultar antes o fabricante quando se depara com a possibilidade do uso de um componente alternativo.
AJUSTES DE MÁQUINA: O CORRETO E O NEM TANTO
Quanto aos Ajustes de Máquina, muito já se falou sobre o que os causam. Mas, vamos enumerar alguns pontos cruciais relacionados a eles:
- Falta de Insumos – Nem sempre os insumos são substituídos, forçando a “criatividade” do operador para dar continuidade a produção, tipo um calço de madeira aqui, um arame amarrado ali etc. Como não existe código de parada para “arrumar uma gambiarra”, ele o aponta simplesmente como “Ajuste de Máquina”. A metalização está com problema, desplacando zinco ou apagando constantemente a tocha? Vai-se produzindo e separando o refugo. O gás acetileno para metalização não foi trocado e o operador acabou utilizando o acetileno de solda mesmo! Ou seja, alguém aplicou o conceito de Custo x Benefício. Mas…
- Manutenção – OK! A manutenção realizada não satisfez a necessidade. Por exemplo, foi feita a revisão da máquina, e o alinhamento dos encostos dos castelos foi esquecido. A chapa fica virando no ferramental, e traz consequências para a solda (desencontro de bordas), além de perfil quadrificado (torção e solda no canto). Toda hora o operador fica ajustando os apertos dos castelos da formação e calibração e das cabeças turcas. Aí, simplesmente ele reduz a velocidade da formadora, e para a toda hora. E ele aponta como Ajuste de Máquina!
- Problemas na Matéria-prima – O operador nota que a cada passagem de emenda, o tubo fica torcido, e aí jugal que tem que ser feito um ajuste na potência da solda. Na verdade, as pontas da bobina têm variação de espessura que comprometem os ajustes. As bobinas têm que ser inspecionadas no seu recebimento e no processamento (slitter). Variações acima da tolerância devem ser, no mínimo, identificadas para serem acompanhadas, ou segregadas nos processos posteriores. Outro fato não perceptível nos processos anteriores é a composição química do aço que, combinada com suas propriedades mecânicas, é exatamente o que determina seu comportamento na conformação e na solda. Então, o PCP deve agrupar as Ordens de Corte preferencialmente por corrida. Isso reduzirá o tempo de ajuste de máquina e as perdas de matéria-prima.
- Setup ou Montagem – Normalmente, todo setup é seguido por um ajuste, pois alguns dos posicionamentos da máquina somente são obtidos com a chapa em movimento: por exemplo, o endireitamento do tubo. A falta de um Plano de Montagem contendo as posições de ajustes de cada bitola deixa o processo totalmente na mão do operador, na base da “tentativa-e-erro”. Também não é raro se colocar um rolo de ferramenta em posição errada. Não se deve nem mesmo negligenciar o uso correto do primeiro rolo de breakdown, que é adequado a certa faixa de espessura. (Ver figura 3). Ao fazer isso, acaba se gerando uma formação inadequada, o que leva o problema para a solda, com a subsequente redução da velocidade de máquina. Aí, o operador fica desesperadamente ajustando os castelos, e reporta como “Ajuste de Máquina” os tempos perdidos. E isso sem falar da geração de desvios da qualidade.
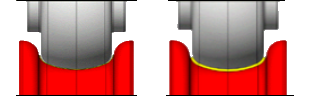
Figura 3 – rolos de espessura
CONCLUSÃO
Uma análise criteriosa dos problemas operacionais, utilizando indicadores de produtividade, é extremamente esclarecedora. A verificação em chão de fábrica, e a elaboração de um plano de ação com a investigação correta das causas responsáveis pelas paradas e perdas – além da identificação das necessidades de treinamento –, certamente trarão bons resultados. Ressalte-se que o objetivo não é “caçar bruxas”, mas, sim, buscar a causa “raiz” dos problemas, e permitir uma solução eficaz.
*CONDEMIR SILVA FILHO é engenheiro e consultor, titular da CSF Consultoria com larga experiência na gestão de fábricas de tubos e centros de serviços.
NOTA DO EDITOR: A primeira parte deste artigo foi exibida na edição de outubro/2024 da revista Siderurgia Brasil. |
[1] Roll-Kraft – Welded Tube Mill Alignments – no cabeçalho de seu folder para alinhamento de formadoras de tubo e perfiladeiras.