Visando se adequar às metas de redução de emissões em todo o mundo, a Vale testou com sucesso um novo tipo de briquete de minério de ferro, adaptado para a rota de redução direta, que irá contribuir para a descarbonização da produção do aço. O novo tipo de briquete emite cerca de 80% menos CO2 em relação às pelotas na sua fabricação, abatendo as emissões diretas e indiretas (escopos 1 e 2) da empresa. O briquete também pode ser utilizado como carga para alto-forno (BF-BOF). A redução direta é uma das rotas utilizadas na produção de aço. Ela é considerada mais “limpa” do que a rota de alto-forno, porque utiliza gás natural em vez de coque – um insumo obtido a partir do carvão mineral, emitindo menos carbono e outros Gases de Efeito Estufa (GEE).
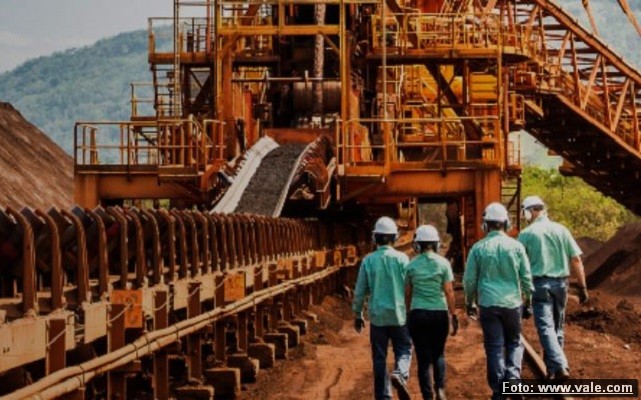
Nos últimos meses, a Vale acelerou o desenvolvimento do novo tipo de briquete destinado a essa rota. Até o momento foram realizados sete testes experimentais em plantas de diferentes clientes nas Américas. Os testes realizados até o momento são conhecidos como “basket” (de cesta, em inglês). Pequenas quantidades de briquete e pelota foram colocados lado a lado em cestas, que alimentaram os reatores. Estudos mostram que para cada tonelada de aço produzido no alto-forno são emitidas duas toneladas de CO2, enquanto na redução direta a emissão de carbono cai para 0,6 a 1 tonelada.
Em um dos testes realizados, por exemplo, o novo produto apresentou um desempenho superior à pelota em metalização , alcançando um teor de ferro metálico de cerca de 98%, enquanto a pelota chegou a 95%. Esse resultado indica que o novo tipo de briquete pode melhorar a produtividade dos clientes siderúrgicos. O próximo passo no desenvolvimento do briquete de redução direta é realizar os testes industriais, que deverão ter início já no mês de junho, em um reator de um cliente na América do Norte.
Anunciado pela Vale em 2021, após cerca de 20 anos de desenvolvimento, o briquete é produzido a partir da aglomeração a baixas temperaturas frio de minério de ferro utilizando uma solução tecnológica de aglomerantes, que confere elevada resistência mecânica ao produto final. Portanto, emite menos poluentes e GEE quando comparado aos processos tradicionais de aglomeração (pelotização e sinterização).
Fonte: Assessoria de imprensa Vale