Analisando os novos tipos de aços encontrados no mercado, denominados ARBL – Alta Resistência e Baixa Liga – percebeu-se que eles apresentam um Coil-Break ou uma ruptura, ou quebra de bobina, muito acentuada.
Claudio Flor*
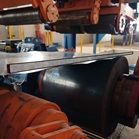
As novas ligas de aços, principalmente os denominados ARBL (Alta Resistência e Baixa Liga) que alteraram as formações nas bobinas evidenciaram dificuldades no processo no desenrolamento ou desbobinamento.
As quebras de bobina Coil-Break assim denominada, são defeitos oriundos das deformações plásticas localizadas e que resultam em uma flexão incompleta durante o processo de desenrolamento (à frio) em faixas periódicas. (figura 1)
Isto decorre em função das variações de espessura, largura, tensão de escoamento. Os processos em fornos de homogeneização na aciaria (denominados de fornos à vácuo) ou resfriamento controlados, apresentam custos elevados, porém seriam uma primeira solução para evitar o acréscimo das “Tensões Internas” das bobinas que resultam em retrabalhos após as configurações das peças.
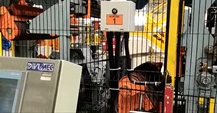
Coil-Break durante muito tempo foi objeto de estudo e observação das consequências dos efeitos de laminação dos metais na concepção de bobinas que produzem impactos durante o desenrolamento em linhas de processamento subsequentes. (figura 2)
Um modelo de elementos finitos serviu de análise evidenciando zonas resultantes com diferentes deformações elasto-plásticas localizadas em diferentes pontos da bobina.
Também e ainda em evidência, outros fatores foram os pontos encontrados periodicamente no diâmetro da bobina (inicial e final), ou entre a superfície externa (figura 3) e interna da tira (tração externa e compressão na interna).

Os defeitos de laminação
Deduziu-se então que o Coil-Break são consequências causadas pelas Tensões Residuais pelos diferentes pontos de Limite de Escoamento ou Alongamento em diferentes zonas ao longo de uma bobina. E para completar temos ainda os diferentes defeitos de laminação.
Observamos que no caso das ARBL (Aços de Alta Resistência e Baixa Liga) apresentam um Coil-Break acentuado.
Estudos comprovam que o Rolo “Anti Coil-Break” minimiza os efeitos durante o desenrolamento sob tensão. Ainda há experiências nas definições, como o diâmetro deste rolo e seu ângulo de aplicação, em função das variáveis: espessura “range”, diâmetro da bobina (externo e interno), tensão de desenrolamento e as características mecânicas do material.
Conclusão: Rolo Anti Coil-Break
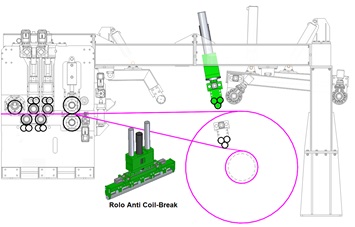
O aumento da diferença de deformação entre as partes do meio e a borda da bobina são amenizados pelo uso do Rolo Anti Coil-Break.
As quebras de bobina ou os Coil-Breaks (figura 4) se alteram ao longo da operação pela variação de largura, espessura e a tensão de escoamento normal durante o desenrolamento. O Rolo reduz esta quebra (queda de tensão) de níveis entre 30% para até 2%.
A redução das variações de diâmetro e da borda sob tração deve-se a redução do grau da curvatura de desenrolamento. Isto auxilia aos próximos equipamentos subsequentes (normalmente a Pré-Endireitadeira) a absorver as concentrações de tensões ao longo da chapa.
O ângulo e a força de ataque do Rolo Anti Coil-Break são empíricos seguem em cálculo e experimento exaustivos.
*Claudio Pereira Flor é engenheiro e CEO da Divimec, uma das maiores fabricantes nacionais de equipamentos para processamento de aços. Colaborador assíduo de nossa publicação possui mais de 50 anos de experiência no ramo do aço e conta com o desenvolvimento de inúmeros produtos para a siderurgia e metalurgia.
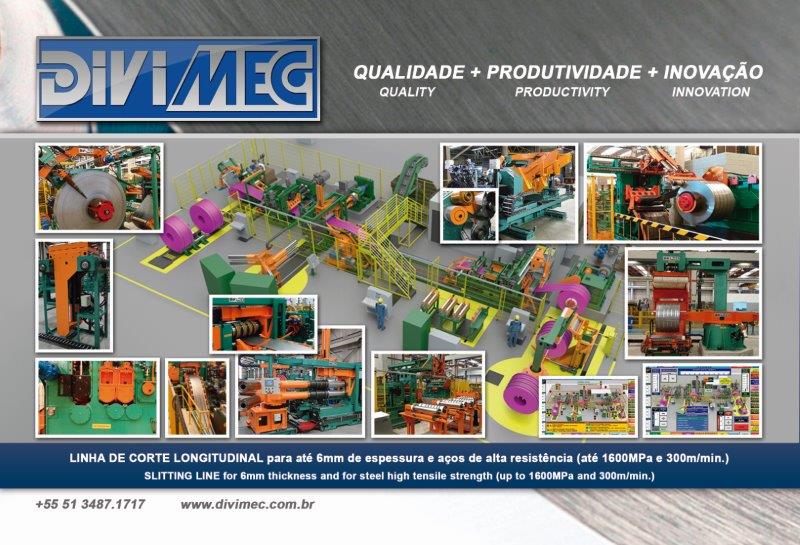