Desde a espada viking “Ulfberht”, a primeira peça de aço conhecida, até os aços de alta resistência e baixa liga, que são os produtos do futuro, muitos caminhos foram percorridos. Conheçam alguns.
Claudio Pereira Flor*
Ainda tratando destes Aços de Alta Resistência e Baixa Liga (ARBL), segue uma “sucinta descrição dos processos produtivos “Inovação” que estão em uso em diferentes culturas (paises e continentes), para operar as bobinas de Aços de Alta Resistência e Baixa Liga (ARBL) por apresentarem tensões residuais elevadas, dificultando as operações subsequentes de corte seja Plasma ou Laser e Dobra ou Conformação.
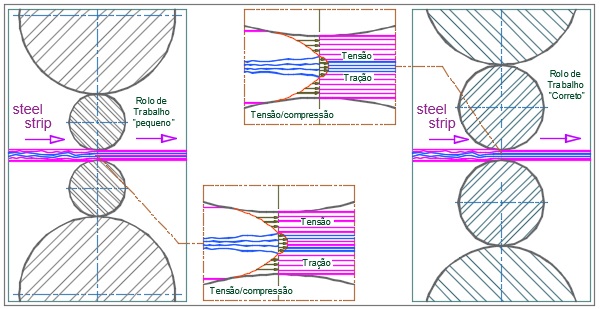
No passado estes problemas eram mais contundentes nas chapas laminadas à frio (aço ou alumínio) e eram resolvidos através das linhas de estiramento “Stretch Levelling Lines”, e hoje também as tensões residuais estão também se apresentando nos laminados à quente – ARBL.
Como mencionado anteriormente foram pesquisados e desenvolvidos três diferentes processos para resolver este problema que são: “Temper-Mill Line”, “Stretch Levelling Line” e Levelling Line”.
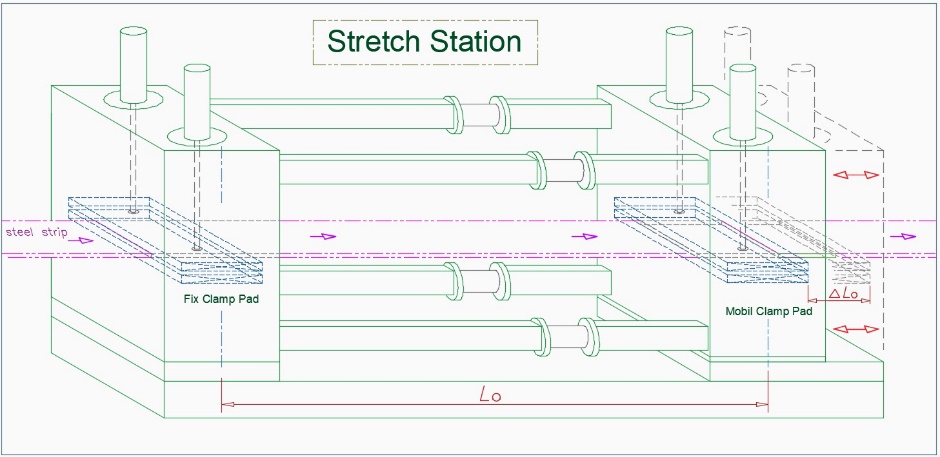
Os ARLB por suas características e por possuirem muitos aditivos apresentam uma tensão residual muito alta e requerem um refinado processo que promova esse alívio.
Podemos acrescenta ainda um mix, ou seja, Temper-Mill ou Stretch Machine adaptado as Linhas de Endireitamento “Levelling Lines” o que aumenta a performance e flexibilidade do “range” de escolha de operação e produtividade.
Para promover um “Alivio de Tensões” (minimo 60 a 80%) além da usual “planicidade” temos os seguintes processos inovados:
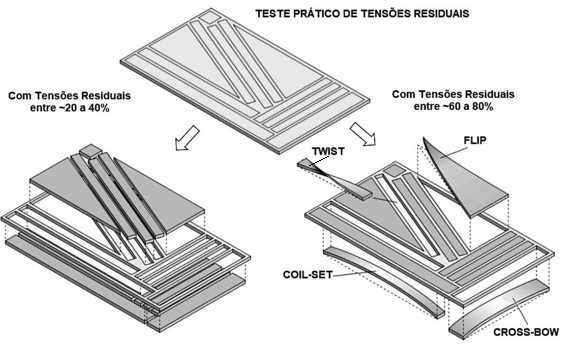
1 – “Temper-Mill Line”.
Este processo consiste em um laminador de “Skin-Pass” na Linha de Corte Transversal. Bastante eficaz ou melhor, o mais eficaz, porém requer um “know-how” aprofundado para determinar os diferentes diâmetros dos rolos laminadores necessários para as diferentes e limitadas espessuras e qualidade do material e a perda dos extremos (sob tensão) das bobinas é um pouco acentuada. Também requer ainda uma ou mais endireitadeiras montadas na linha para melhorar a qualidade da planicidade final. O investimento deste tipo de equipamento é muito alto e limita sua viabilidade em alguns casos para diferentes aços e baixa produção.
Este processo apresenta uma produtividade melhor do que o anterior e perda menor. Também requer uma operação qualificada (conhecimento metalúrgico) e a produtividade também não é muito elevada e o custo de investimento é mais viável e econômico.

Este processo quando em conjunto com uma “Levelling Line” específica existente, tem sua produtividade e custo produtivo próximo da entrega de um produto competitivo.
2 – “Stretch Levelling Line”
Este processo já existente através de “Bridle-Rolls” para bobinas de materiais de fina espessura. Agora, entretanto, em sua nova concepção para materiais mais espessos e de maior resistência (Laminados à quente) através do estiramento até o limite de escoamento foi desenvolvido através de uma “Stretch Station”.
Este processo apresenta uma produtividade melhor do que a anterior e perda menor.
Também requer uma operação qualificada (conhecimento metalúrgico) e uma produtividade relativa não muito elevada e um custo de investimento mais viável e econômico.
Este processo quando em conjunto com processo de uma “Levelling Line” específica existente, tem sua produtividade e custo produtivo próximo da entrega de um produto competitivo.
Obervação: Ambos os processos acima são de amplo domínio e usuais dos norte-americanos sendo que o primeiro já está no Brasil e o segundo muito em breve também estará disponível em nosso mercado.
3 – “Levelling Line”.
Este processo consiste no princípio de prover sucessíveis flexões no material (chapa) de forma que entre na região de deformação plástica atingindo o limite de elasticidade.
Isto propicia um certo alívio de tensões, entretanto em função do diâmetro e distância entre rolos Endireitadores, as “tensões Residuais” são supridas somente entre 60 a 80% das existentes o que são aceitáveis para maioria dos usuários.
Este processo é usual dos europeus, asiáticos e nacional, pelo baixo custo de investimento, melhor produtividade e perdas menores.
A figura abaixo demonstra e constitui a configuração mínima (sempre com corte dinâmico ou seja sem parar o material nas endireitadeiras) de uma linha com estas características.
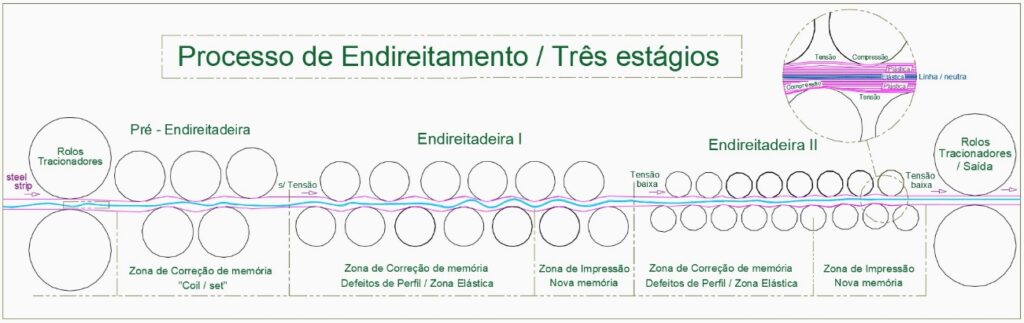
a – Chapas/requisitos
Planicidade e Dimensionamento são os principais requisitos de fornecimento dos “Blanks” e que a maioria dos equipamentos existentes atingem de acordo com o mercado proposto.
Tensões Residuais – Os Blanks devem ser “Livre de tensões residuais internas” (escondidas) de forma que não influenciem na conformação das peças subsequentes.

O Blank ideal não deve ter nenhuma tensão residual interna, entretanto pode haver percentual mínimo admissível (entre 20 a 40%) e para tanto os norte-americanos desenvolveram um método (destrutivo) de medição através do corte em “plasma” ou “laser” com dimensões compatíveis com a aplicação final o que comprova que as Tensões Residuais acima de 60% não apresentam bons resultados finais para a produção de peças.
b – Diagrama da “Tensão – Deformação”
Basicamente todo o provedor de metais, e principalmente do aço, deve ter conhecimento deste Diagrama
Nota do Editor: A primeira parte deste artigo foi exibido na edição anterior da revista Siderurgia Brasil Digital. Veja em https://siderurgiabrasil.com.br/revista/ edição 160 (setembro 2022) e trata das exigências dos aços do futuro.
*Claudio Pereira Flor é diretor-presidente da Divimec Tecnologia Industrial Ltda., fabricante de linhas de corte longitudinal, transversal entre outros.